Dynamic Simulation using UG NX4 Motion Simulation Module
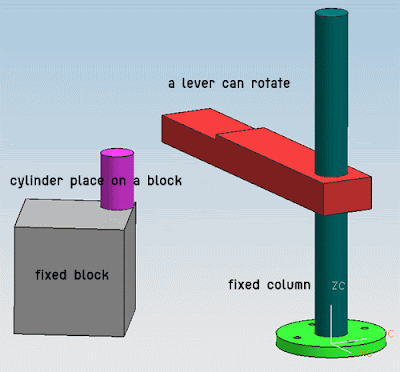
Which software are you using in your mechanical design project? I have been using Solid Edge 3D CAD software for 1-2 years for my mechanical design projects in the past. But now, according to the standardization in my design organization, I have to switch to use Unigraphics software instead, or we call it in short as "UG NX4" (the latest version is NX6). To be honest, at first I still like Solid Edge because I think I can make modeling and assembly in Solid Edge faster and easier than in UG. But one of the good thing for UG is Motion Simulation module that help me simulate the movement of mechanical assemblies before releasing for manufacturing. I know that Solid Edge also has this kind of simulation module, but I didn't have a chance to use (no license). So in this post, I would like to share how easy to set up motion simulation in UG NX4. Let's start with a very simple modeling. I would like to see how the cylinder moves when it is pushed by the rotating l...