V-Belt Drive Design
A belt is a flexible power transmission element that seats tightly on a set of pulleys or sheaves. When the belt is used for speed reduction, the typical case, the smaller sheave is mounted on the high-speed shaft, such as the shaft of an electric motor. The larger sheave is mounted on the driven machine. The belt is designed to ride around the two sheaves without slipping.
The belt is installed by placing it around the two sheaves while the center distance between them is reduced. Then the sheaves are moved apart, placing the belt in a rather high initial tension. When the belt is transmitting power, friction causes the belt to grip the driving sheave, increasing the tension in one side, called the "tight side," of the drive. The tensile force in the belt exerts a tangential force on the driven sheave, and thus a torque is applied to the driven shaft. The opposite side of the belt is still under tension, but at a smaller value. Thus, it is called the "slack side."
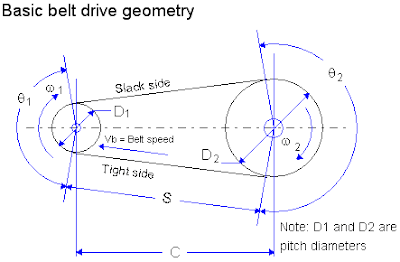
The most widely used type of belt, particularly in industrial drives and vehicular applications, is the V-belt drive. The V-shape causes the belt to wedge tightly into the groove, increasing friction and allowing high torques to be transmitted before slipping occurs. Most belts have high-strength cords positioned at the pitch diameter of the belt cross section to increase the tensile strength of the belt. The cords, made from natural fibers, synthetic strands, or steel, are embedded in a firm rubber compound to provide the flexibility needed to allow the belt to pass around the sheave. Often an outer fabric cover is added to give the belt good durability. The data given in this program are for the narrow-section belts: 3V, 5V and 8V.

The pulley, with a circumferential groove carrying the belt, is called a sheave (usually pronounced "shiv").
The size of a sheave is indicated by its pitch diameter, slightly smaller than the outside diameter of the sheave.

The speed ratio between the driving and the driven sheaves is inversely proportional to the ratio of the sheave pitch diameters. This follows from the observation that there is no slipping (under normal loads). Thus, the linear speed of the pitch line of both sheaves is the same as and equal to the belt speed, vb. Then


This is important for two reasons: You can check the proper belt tension by measuring the amount of force required to deflect the belt at the middle of the span by a given amount. Also, the tendency for the belt to vibrate or whip is dependent on this length.
The contributors to the stress in the belt are as follows:
The factors involved in selection of a V-belt and the driving and driven sheaves and proper installation of the drive are summarized in this section. Abbreviated examples of the data available from suppliers are given for illustration. Catalogs contain extensive data, and step-by-step instructions are given for their use. The basic data required for drive selection are the following:
The belt is installed by placing it around the two sheaves while the center distance between them is reduced. Then the sheaves are moved apart, placing the belt in a rather high initial tension. When the belt is transmitting power, friction causes the belt to grip the driving sheave, increasing the tension in one side, called the "tight side," of the drive. The tensile force in the belt exerts a tangential force on the driven sheave, and thus a torque is applied to the driven shaft. The opposite side of the belt is still under tension, but at a smaller value. Thus, it is called the "slack side."
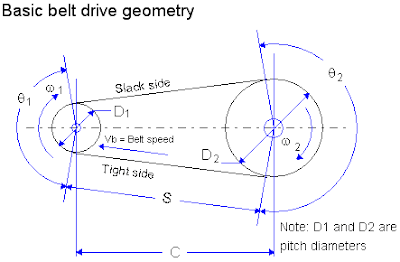
The most widely used type of belt, particularly in industrial drives and vehicular applications, is the V-belt drive. The V-shape causes the belt to wedge tightly into the groove, increasing friction and allowing high torques to be transmitted before slipping occurs. Most belts have high-strength cords positioned at the pitch diameter of the belt cross section to increase the tensile strength of the belt. The cords, made from natural fibers, synthetic strands, or steel, are embedded in a firm rubber compound to provide the flexibility needed to allow the belt to pass around the sheave. Often an outer fabric cover is added to give the belt good durability. The data given in this program are for the narrow-section belts: 3V, 5V and 8V.

The pulley, with a circumferential groove carrying the belt, is called a sheave (usually pronounced "shiv").
The size of a sheave is indicated by its pitch diameter, slightly smaller than the outside diameter of the sheave.

The speed ratio between the driving and the driven sheaves is inversely proportional to the ratio of the sheave pitch diameters. This follows from the observation that there is no slipping (under normal loads). Thus, the linear speed of the pitch line of both sheaves is the same as and equal to the belt speed, vb. Then

The relationships between pitch length, L, center distance, C, and the sheave diameters are
Where: B = 4L - 6.28(D2 - D1)
The angle of contact of the belt on each sheave is
These angles are important because commercially available belts are rated with an assumed contact angle of 180°. This will occur only if the drive ratio is 1 (no speed change). The angle of contact on the smaller of the two sheaves will always be less than 180°, requiring a lower power rating. Note: the angle of wrap on the smaller sheave should be greater then 120°.
The length of the span between the two sheaves, over which the belt is unsupported, is
The length of the span between the two sheaves, over which the belt is unsupported, is

This is important for two reasons: You can check the proper belt tension by measuring the amount of force required to deflect the belt at the middle of the span by a given amount. Also, the tendency for the belt to vibrate or whip is dependent on this length.
The contributors to the stress in the belt are as follows:
- The tensile force in the belt, maximum on the tight side of the belt.
- The bending of the belt around the sheaves, maximum as the tight side of the belt bends around the smaller sheave.
- Centrifugal forces created as the belt moves around the sheaves.
The factors involved in selection of a V-belt and the driving and driven sheaves and proper installation of the drive are summarized in this section. Abbreviated examples of the data available from suppliers are given for illustration. Catalogs contain extensive data, and step-by-step instructions are given for their use. The basic data required for drive selection are the following:
- The rated power of the driving motor or other prime mover
- The service factor based on the type of driver and driven load
- The center distance
- The power rating for one belt as a function of the size and speed of the smaller sheave
- The belt length
- The size of the driving and driven sheaves-- As a guide this software suggests selecting a standard input driving sheave that produces a belt speed of 4000 ft/min.
- The correction factor for belt length
- The correction factor for the angle of wrap on the smaller sheave
- The number of belts
- The initial tension on the belt
- Adjustment for the center distance must be provided in both directions from the nominal value. The center distance must be shortened at the time of installation to enable the belt to be placed in the grooves of the sheaves without force. Provision for increasing the center distance must be made to permit the initial tensioning of the drive and to take up for belt stretch. Manufacturers' catalogs give the data. One convenient way to accomplish the adjustment is the use of a take-up unit.
- If fixed centers are required, idler pulleys should be used. It is best to use a grooved idler on the inside of the belt, close to the large sheave. Adjustable tensioners are commercially available to carry the idler.
- The nominal range of center distances should be
- The angle of wrap on the smaller sheave should be greater than 120°.
- Most commercially available sheaves are cast iron, which should be limited to 6 500-ft/min belt speed.
- Consider an alternative type of drive, such as a gear type or chain, if the belt speed is less than 1,000 ft/min.
- Avoid elevated temperatures around belts.
- Ensure that the shafts carrying mating sheaves are parallel and that the sheaves are in alignment so that the belts track smoothly into the grooves.
- In multibelt installations, matched belts are required. Match numbers are printed on industrial belts, with 50 indicating a belt length very close to nominal. Longer belts carry match numbers above 50; shorter belts below 50.
- Belts must be installed with the initial tension recommended by the manufacturer. Tension should be checked after the first few hours of operation because seating and initial stretch occur.
Most manufacturers offer two kinds of belts in each cross section. The ones with the "X" are cog belts, and if there is no "X", it is of plain construction. Both types have the same cross sectional dimensions and will therefore fit in the same sheave.
Comments