Finite Element Analysis (FEA): Introduction
The following four-article series was published in a newsletter of the American Society of Mechanical Engineers (ASME). It serves as an introduction to the recent analysis discipline known as the finite element method (FEM). The author is an engineering consultant and expert witness specializing in finite element analysis.
FINITE ELEMENT ANALYSIS: Introduction
by Steve Roensch, President, Roensch & Associates
First in a four-part series
Finite element analysis (FEA) is a fairly recent discipline crossing the boundaries of mathematics, physics, engineering and computer science. The method has wide application and enjoys extensive utilization in the structural, thermal and fluid analysis areas. The finite element method is comprised of three major phases:
(1) pre-processing, in which the analyst develops a finite element mesh to divide the subject geometry into subdomains for mathematical analysis, and applies material properties and boundary conditions.
(2) solution, during which the program derives the governing matrix equations from the model and solves for the primary quantities.
(3) post-processing, in which the analyst checks the validity of the solution, examines the values of primary quantities (such as displacements and stresses), and derives and examines additional quantities (such as specialized stresses and error indicators).
The advantages of FEA are numerous and important. A new design concept may be modeled to determine its real world behavior under various load environments, and may therefore be refined prior to the creation of drawings, when few dollars have been committed and changes are inexpensive. Once a detailed CAD model has been developed, FEA can analyze the design in detail, saving time and money by reducing the number of prototypes required. An existing product which is experiencing a field problem, or is simply being improved, can be analyzed to speed an engineering change and reduce its cost. In addition, FEA can be performed on increasingly affordable computer workstations and personal computers, and professional assistance is available.
It is also important to recognize the limitations of FEA. Commercial software packages and the required hardware, which have seen substantial price reductions, still require a significant investment. The method can reduce product testing, but cannot totally replace it. Probably most important, an inexperienced user can deliver incorrect answers, upon which expensive decisions will be based. FEA is a demanding tool, in that the analyst must be proficient not only in elasticity or fluids, but also in mathematics, computer science, and especially the finite element method itself.
Which FEA package to use is a subject that cannot possibly be covered in this short discussion, and the choice involves personal preferences as well as package functionality. Where to run the package depends on the type of analyses being performed. A typical finite element solution requires a fast, modern disk subsystem for acceptable performance. Memory requirements are of course dependent on the code, but in the interest of performance, the more the better, with 512 Mbytes to 8 Gbytes per user a representative range. Processing power is the final link in the performance chain, with clock speed, cache, pipelining and multi-processing all contributing to the bottom line. These analyses can run for hours on the fastest systems, so computing power is of the essence.
One aspect often overlooked when entering the finite element area is education. Without adequate training on the finite element method and the specific FEA package, a new user will not be productive in a reasonable amount of time, and may in fact fail miserably. Expect to dedicate one to two weeks up front, and another one to two weeks over the first year, to either classroom or self-help education. It is also important that the user have a basic understanding of the computer's operating system.
FINITE ELEMENT ANALYSIS: Introduction
by Steve Roensch, President, Roensch & Associates
First in a four-part series
Finite element analysis (FEA) is a fairly recent discipline crossing the boundaries of mathematics, physics, engineering and computer science. The method has wide application and enjoys extensive utilization in the structural, thermal and fluid analysis areas. The finite element method is comprised of three major phases:
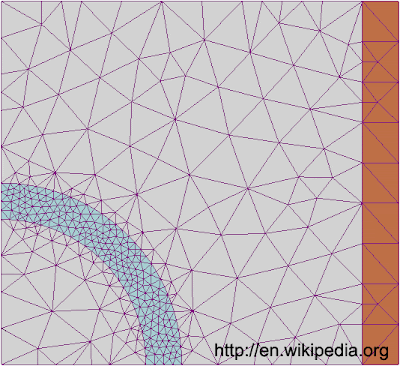
(2) solution, during which the program derives the governing matrix equations from the model and solves for the primary quantities.
(3) post-processing, in which the analyst checks the validity of the solution, examines the values of primary quantities (such as displacements and stresses), and derives and examines additional quantities (such as specialized stresses and error indicators).
The advantages of FEA are numerous and important. A new design concept may be modeled to determine its real world behavior under various load environments, and may therefore be refined prior to the creation of drawings, when few dollars have been committed and changes are inexpensive. Once a detailed CAD model has been developed, FEA can analyze the design in detail, saving time and money by reducing the number of prototypes required. An existing product which is experiencing a field problem, or is simply being improved, can be analyzed to speed an engineering change and reduce its cost. In addition, FEA can be performed on increasingly affordable computer workstations and personal computers, and professional assistance is available.
It is also important to recognize the limitations of FEA. Commercial software packages and the required hardware, which have seen substantial price reductions, still require a significant investment. The method can reduce product testing, but cannot totally replace it. Probably most important, an inexperienced user can deliver incorrect answers, upon which expensive decisions will be based. FEA is a demanding tool, in that the analyst must be proficient not only in elasticity or fluids, but also in mathematics, computer science, and especially the finite element method itself.
Which FEA package to use is a subject that cannot possibly be covered in this short discussion, and the choice involves personal preferences as well as package functionality. Where to run the package depends on the type of analyses being performed. A typical finite element solution requires a fast, modern disk subsystem for acceptable performance. Memory requirements are of course dependent on the code, but in the interest of performance, the more the better, with 512 Mbytes to 8 Gbytes per user a representative range. Processing power is the final link in the performance chain, with clock speed, cache, pipelining and multi-processing all contributing to the bottom line. These analyses can run for hours on the fastest systems, so computing power is of the essence.
One aspect often overlooked when entering the finite element area is education. Without adequate training on the finite element method and the specific FEA package, a new user will not be productive in a reasonable amount of time, and may in fact fail miserably. Expect to dedicate one to two weeks up front, and another one to two weeks over the first year, to either classroom or self-help education. It is also important that the user have a basic understanding of the computer's operating system.
Comments